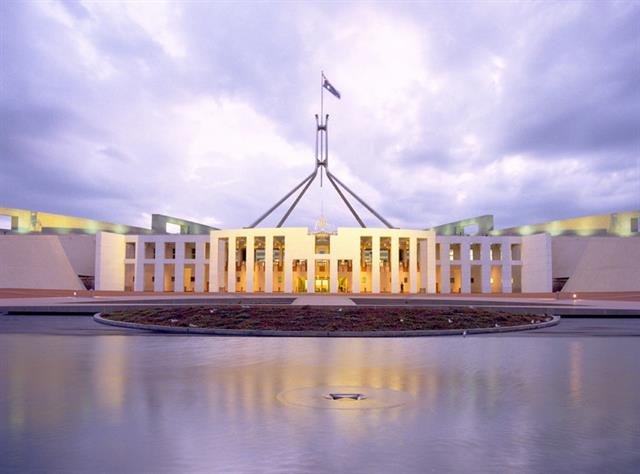
Materials handling showed its resilience Down Under, with significant fleet renewals and a number of automation projects completed in the past year. Allan Leibowitz recaps on a busy year in Australasia.
Materials handling in Australia was buoyed by strong performance in the broader economy. As reported at the start of the year, a $225 billion national commitment to infrastructure projects from state governments, delivered over the next four years, was warmly welcomed by the business community, including the Australian Logistics Council.
“Investment in infrastructure combined with a collaborative approach with industry to planning for preservation of freight lands and corridors are key to a successful and functioning future economy,” said Kirk Coningham, CEO of ALC. “Providing clarity and security of the pipeline encourages investment.”
Analysis in the first quarter revealed that forklifts were among the fastest-growing industrial equipment purchases in Australia.
NAB statistics showed businesses across Australia were purchasing new equipment and vehicles in record numbers as companies embraced the strongest market conditions seen in years.
In a briefing around that time, Combilift founder Martin McVicar noted record Australian sales for the Irish manufacturer in the first quarter of 2021, and he told Forkliftaction News he was confident the growth would be sustained.
Business confidence got a boost from the Federal Budget in May, with the Australian Chamber of Commerce and Industry particularly pleased with the increased investment in skills.
The ALC praised the investments in the National Freight Data Hub and the National Heavy Vehicle Regulator announced in the budget.
Forklift dealers were already benefiting from instant investment write-offs, and business groups were pleased to see a budget extension of the arrangements.
The budget measures meant that businesses with a turnover or income of less than $5 billion could immediately write off the cost of assets they first used or installed by 30 June 2023.
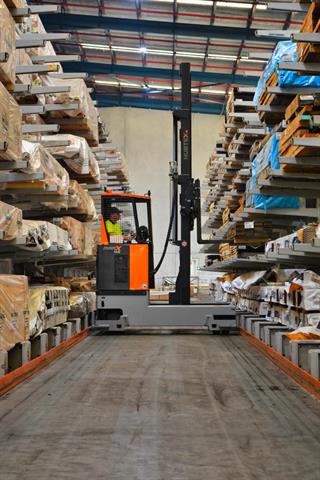
Fleet expansion
Through the year, there were many reports of equipment investment and fleet expansions.
In July, Arcadian Organic & Natural Meat Co. located on the New South Wales Central Coast changed its entire fleet of materials handling equipment to Toyota Material Handling Australia products.
The new fleet consists of four Toyota LWE180 electric-powered pedestrian pallet jacks with maintenance-free batteries, two Toyota LHM230 Quick Lifter hand pallet jacks, two Toyota 8FBE18 counterbalance three-wheel electric forklifts, a Toyota 7300 double-deep reach forklift and a Toyota 8FBR16 moving-mast reach forklift for cold storage warehousing.
In August, Britton Timbers switched to electric sideloaders at its distribution centres in Tasmania, Melbourne, Sydney and Brisbane.
The company had found significant gains in storage capacity with its existing sideloader fleet, but the machines in use were LPG which caused problems inside the warehouse with noise and pollution, as well as reliability issues.
In September, Australian confectionary company Robern Menz commemorated its success by decking out one of its Toyota Material Handling Australia (TMHA) forklifts with a Violet Crumble-themed paint job. Robern Menz uses a fleet of 14 different TMHA machines to run its business, and got its latest machine prepared with distinctive Violet Crumble livery.
Toyota also supplied Western Australian manufacturer Funky Monkey Bars with two 32-8FG25 forklifts, a 32-8FGJ35 forklift and an RRE160H reach forklift with 7,000 mm lift height.
In October, Kalmar received a large repeat order of six Kalmar Automatic Stacking Cranes (ASCs) from Victoria International Container Terminal (VICT). The new Kalmar ASCs will enable VICT to expand its current capacity at the Port of Melbourne at Webb Dock East.
Supplier developments
Cascade Corporation started the year with a distribution agreement with Meijer Handling Solutions for Meijer’s Kooi line of products in Australia.
Meijer’s Kooi product offerings include the well-known Kooi Reachforks for double deep racking (hydraulic and manual versions), Rollerforks for slipsheet and pallet handling, Single Height Shift System, Mast Height Extension systems and several other value-oriented offerings.
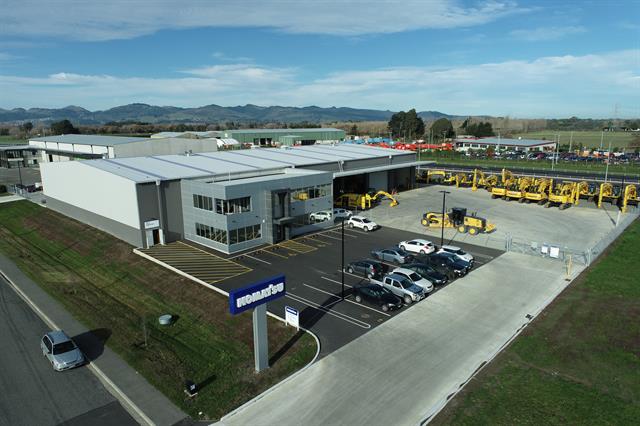
In March, Big Joe Forklifts announced its return to Australian shores after several years’ absence. Big Joe are sold through Koala Forklifts.
Komatsu New Zealand officially opened its new South Island Hub facility in Christchurch in the first half of the year. The state-of-the-art facility, which was commissioned in mid-2020, offers greatly enhanced service and support capabilities for Komatsu customers throughout the South Island.
In September, Hino Australia officially opened its new 9,272 sqm state-of-the art purpose-built parts distribution centre in Sydney’s Horsley Park. Hino worked with a leading international storage solutions provider to design and install a storage solution that includes small parts storage, through to single and double depth pallet racking and open-faced cantilever racking.
In November, Bolzoni appointed MARS Engineers as its exclusive dealer in Western Australia. The company had worked closely with Bolzoni Auramo and Meyer products for over seven years in a technical, engineering and sales capacity.
Automation activity
There were a number of significant automation developments in 2021, starting with Lion Australia future-proofing supply chain and manufacturing operations at its Tooheys Brewery in Lidcombe, NSW with Dematic Automated Guided Vehicles (AGVs).
“The implementation of AGVs was part of a widespread initiative to optimise operations within the Tooheys Brewery and across the entire business,” says Tim Symonds, packaging manager at Tooheys.
Australia’s oldest family-owned meat processor, John Dee, commenced the implementation of the Dematic Multishuttle Meat Buffer Storage and Handling System at its Queensland abattoir in Warwick to meet growth in customer demand and streamline operations in sub-zero conditions.
Also in May, Australian footwear retailer Spendless Shoes began to implement Manhattan Associates’ Warehouse Management Solution (WMS) to reinvent its out-dated supply chain operations and gain the flexibility to adapt to current and future changes in the retail market. Spendless Shoes’ decision to introduce the Manhattan solution to its distribution centre in Adelaide, South Australia stemmed from its previous challenges with not having company-wide visibility of inventory, as well as the ongoing changes associated with the pandemic, such as growth in online sales and lockdowns.
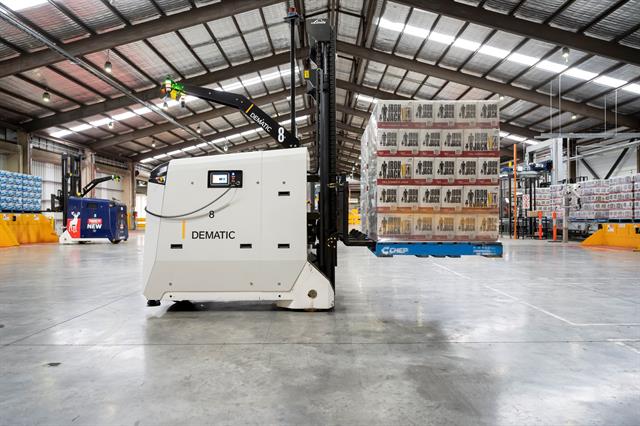
Meanwhile, Australian retailer Woolworths announced plans to construct a new automated customer fulfilment centre (CFC) in Auburn, New South Wales to better serve the online grocery needs of Western Sydney customers. The facility will be built in partnership with Knapp, whose automation technology will help Woolworths’ personal shoppers pick and dispatch up to 50,000 home deliveries a week in Western Sydney.
In June, Thomas Foods International prepared to deploy Dematic automation at its new meat processing facility in Murray Bridge, South Australia. After its original processing plant was destroyed by fire in 2018, Thomas Foods International made a commitment to rebuild the plant “bigger, better and stronger”. The new flagship facility, currently under construction, will offer a future-proof, fully optimised supply chain to service local and global demand for decades to come.
A new fully automated purpose-built distribution centre, powered by state-of-the-art technology, including driverless forklifts, opened in Truganina in Melbourne’s west in July. Built by Toll for Mars Wrigley Australia, the warehouse uses 17 automated guided vehicles (AGVs) to manage most of the workload. The AGVs interface with the existing warehouse management system to track product flow from production to storage and all the way through to dispatch. One of the first of its kind in Australia, the new centre can house 50,000 pallets, holding the equivalent of more than 700 million Mars bars.
Meanwhile, as part of its network optimisation strategy to increase its competitiveness in the pharmaceutical industry, leading Australian pharmaceutical wholesaler Sigma Healthcare automated operations at its new Perth and Brisbane distribution centres (DCs) with the Dematic Goods-to-Person (GTP) Picking Solution.
Sigma selected the fully automated Dematic solution as the central system to improve operational efficiencies at its two new DCs. Sigma’s switch to automation stemmed from previous supply chain challenges experienced with legacy systems deployed at other DCs, which were restricting the ability to continue to improve service delivery to customers.
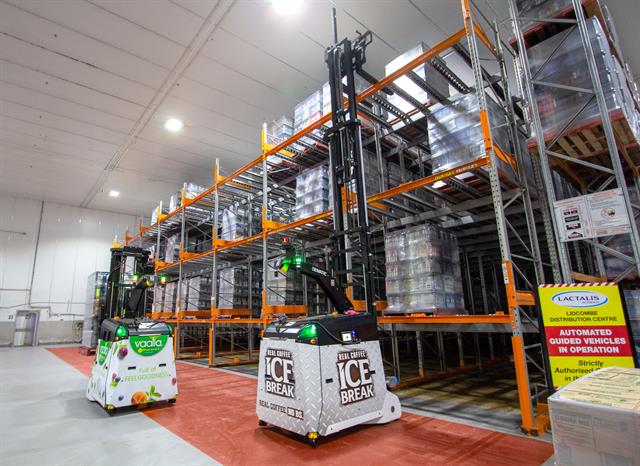
In October, Amazon revealed that its new Sydney warehouse will double the online retailer’s operational footprint in Australia and will rely on Robotic Drive Units to boost productivity.
The robots do much of the heavy lifting, picking up mobile shelves and bringing them to employees, who check and pack the items before they are sent on their way, according to an article in the Engineers Australia journal, Create.
In October, Lactalis Australia, part of global dairy producer Lactalis, invested in an additional AGV for its fleet, in a bid to boost warehouse-wide efficiency at its Lidcombe milk site in NSW. With the addition of a fifth Dematic AGV to operations, Lactalis is now able to expand automation to more areas within the warehouse.
Later, Daikin switched on the ignition to Manhattan Associates’ Manhattan SCALE warehouse management solution (WMS) at its new distribution centre in Warwick Farm, Sydney. Manhattan SCALE serves as an all-encompassing automated warehouse solution to optimise manufacturing, fulfilment and dispatch operations at Daikin Park – the largest air conditioning DC in Australia. By offering end-to-end visibility and flexible control over DC operations, the new solution allows Daikin to better manage and expand operations to meet the huge growth the company has experienced in Australia over recent years.
Safe and sound
As usual, October was designated as National Safe Work Month. Safe Work Australia chose the theme “Keeping all workers safe”, stressing that everyone has a responsibility to manage hazards and risks at their workplace.
The agency updated its national work health and safety statistics, providing important evidence on the state of work health and safety in Australia.
The safety agency noted that 194 people were fatally injured at work in 2020, a 50% drop in the fatality rate since 2007.
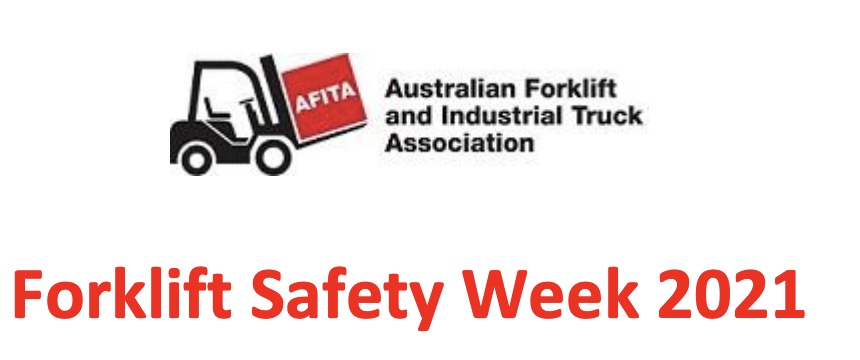
Safe Work reported that 96% of worker fatalities in 2020 were male and vehicle collisions accounted for 41% of all 2020 worker fatalities. Machinery operators and drivers, including forklift drivers, had the highest number of fatalities by occupation (67 fatalities) in 2020.
Forklift accidents in 2021 included a man seriously injured after his foot was run over by a forklift in Christchurch, New Zealand. The man was trapped under a forklift at Meadow Fresh, a leading New Zealand dairy products manufacturer.
In October, the District Court of New South Wales fined an employer after a worker was seriously injured when an excavator bucket slipped off the tines of a forklift. The case dates back to an accident in February 2018. The Court reduced a $100,000 fine by 25% to reflect the defendant’s guilty plea and ordered the defendant pay the prosecutor’s costs in the amount of $30,000.

In September, a man was charged with drunkenly driving a forklift and causing the death of another man riding on the vehicle when it rolled in Middlemount.
The driver, a 42-year-old Sarina man, was charged with driving without due care causing death, consuming liquor while driving, and driving with a passenger in a vehicle not designed for that.
End note
One of the social media highlights of 2021 was a TikTok user who posted bizarre footage of a forklift at a fast food drive-thru. The incident occurred in Melbourne, when the tradesman was spotted driving his forklift through a Hungry Jack’s drive-thru to grab a meal.
Discussion about this post