Botsync’s MAG automatic mobile robot
The autonomous mobile robots (AMRs) industry has grown in the past decade, driven by e-commerce. Companies in the sector has adopted AMRs to support the rapid movement of products within warehouses and around the world. This has helped them keep up with the competition, enhance productivity and increase efficiency.
Four Singapore-based robotics enthusiasts sensed an opportunity in this space early on and started Botsync, a heavy-duty, intelligent, industrial AMR startup. The startup envisions becoming the go-to automation solution provider for internal logistics movement in the APAC market.
Botsync was founded in 2017 by Nikhil Venkatesh (CTO), Prashant Trivedi (Chief Commercial Officer), Singaram Venkatachalam (COO), and Nambiar (CEO) — all graduates of Singapore’s Nanyang Technological University — to turn their passion into an industrial breakthrough.
Its flagship product is MAG, a deep learning engine-powered AMR that can autonomously navigate the operating site to transfer loads of up to 1,500 kg, utilising the base map and multiple integrated sensors. The product comes in two variants: MAG300 and MAG1000.
Also Read: Why robotics is just entering its prime phase
Botsync has also developed Volta, a compact indoor mobile robot for ROS (robot operating system) learning, teaching and research, and Copernicus, an all-terrain mobile robot for outdoor robotics research or solution prototype.
Wong Fong Engineering’s strategic investment
Last week, Botsync announced a pre-Series A funding round from Wong Fong Engineering, SEEDS Capital, Angel Central, VentureCatalysts, Amit Pachisia, ZB Capital, Iterative, Locus Ventures, Funderbeam, Nalin Advani and Roger Crook to support the “growing demand”.
The strategic investment by Wong Fong Engineering, a leading Singapore-based industrial machinery maker, is particularly crucial.
“Wong Fong Engineering has been a strategically aligned investor since our seed round,” says Nambiar. “Our strength as a company lies in our ability to design and develop intelligent systems. However, providing heavy-duty solutions requires an equally strong background and capabilities in engineering to provide high-quality solutions to our users. In this respect, Wong Fong has been a great partner to us, providing the collective engineering and production capability to improve the technical quality of our offerings,” he adds.
With offices in Singapore and Bangalore, Botsync plans to deploy MAG AMRs across Asia over the next two years. In addition to expanding to these two markets, it also aims to build a network of partners with local offices to drive commercial expansion in countries like Malaysia and Thailand. These plans are already underway in Thailand, and the firm looks to do the same in Malaysia moving forward.
Besides deploying its flagship product, Botsync will enhance syncOS. This no-code interface allows site managers with no formal or technical background in robotics to build customised and complex workflows. This removes the necessity of recruiting and building an expensive in-house robotics task force.
“Our AMRs are versatile as they do not require infrastructural elements to navigate. Users can explore and fully design solutions with the syncOS platform simply by dragging and connecting building blocks on the interface,” explains Nambiar.
AMRs becoming prevalent
In Nambiar’s opinion, with the increasing supply chain challenges, the usage of AMRs to drive productivity in intralogistics has become prevalent, especially in the manufacturing and hospitality industry.
Three factors drive this usage: Firstly, the use of automated guided vehicles (AGVs) to support production lines has been phasing out. Companies in the automotive and electronics sectors now prefer to transit to AMR technology to drive their lines.
Secondly, there has been a greater push for digitalisation and visibility across the supply chain down to the manufacturing floor to improve companies’ response to supply chain shocks. A well-designed AMR solution integrated with the right tools can enhance this visibility on the production floor for users, giving them a greater understanding of where and how their inventory is used.
Lastly, the limited availability of forklift drivers has increasingly pushed companies to rely on AMRs. For operations that involve the movement of heavy materials that weigh close to one ton, forklifts continue to be the primary means to drive the intralogistics processes. With the greater availability of gig economy-driven jobs, companies now find it challenging to attract and then train and certify forklift drivers in shorter intervals due to higher retrenchment rates.
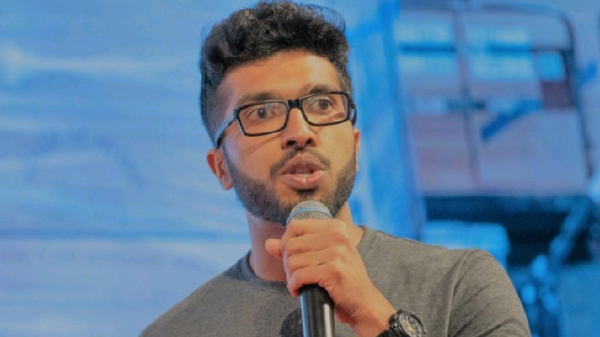
Botsync Co-Founder and CEO Rahul Nambiar
With the decreasing sensor costs and greater computing power, unit costs of robots have come down over the past decade. This has opened new opportunities for the sector to capitalise on and build better, more autonomous, flexible and cost-efficient robotic solutions.
“Having said that, lower costs and a cost reduction-based value proposition alone will not suffice to drive the adoption of AMRs.
Greater interoperability between the different robotics solutions for easier integrations and the ability to operate in more challenging environments will be instrumental for developments like low-code or no-code systems. This will allow users to derive more significant value from robotics, like overall process improvement and supply chain visibility, to justify their investment in robotics. Such initiatives can and will help drive the robotics density in the region to higher levels,” Nambiar explains.
Also Read: Southeast Asia paves the way for new value in robotics
Nonetheless, the AMR industry has yet to see significant growth. Several vital challenges prevent the growth.
“One significant challenge is that investment in robots is often justified by how much can be saved in labour costs. For example, lower labour costs in India remain a key factor in ensuring sufficient throughput is delivered while maintaining reasonable ROI timelines,” he remarks.
“However, in Singapore and Thailand, the adoption of robotics is higher than wage levels predict. While labour cost is one factor, the adoption of robotics differs based on the industry and national goals or plans around robotic development and adoption,” the CEO adds.
Another key challenge is the quality of the infrastructure and processes within a facility. Currently, many facilities in Asia run manual operations without a clear breakdown of processes. This impedes robotics implementation as there is no repeatable process to automate, especially in intralogistics and material handling.
“Additionally, the building infrastructure is crucial to support the logistics and operational service of AMRs, for instance, the flooring condition. Firms that cannot meet these quality standards may miss out on the opportunity to adopt robotic solutions,” he elaborates.
Pinning hope on India
For Botsync, AMRs’ adoption by e-commerce companies in India presents great opportunities. They use the systems to reduce operational costs and improve their overall delivery time.
“It has been amazing to see the traction in other sectors, particularly within the manufacturing space. More active conversations on AMR installations have started in companies of automotive and electronics sectors and sectors of other machines with greater importance placed on improving overall process standards, operating conditions and inventory visibility, driving increased adoption,” Nambiar notes.
The AMR market is still in its infancy, with less than 4 per cent of total potential sites globally today with an AMR implementation, thus presenting a huge growth potential within this sector. Intralogistics in the manufacturing sector, particularly within the automotive, electronics and machine component space, will be one of Botsync’s primary targets in this region. The third-party logistics space will be equally attractive in the future for us as we expand our product portfolio and system capabilities.
Over the past 18 months, the company grew from 15 employees to 30. During that period, it also expanded its business in India and moved to a 15,000-square feet office facility in Bangalore to support product manufacturing and testing and set up a dedicated sales and project team.
Nambiar admits that challenges such as relying on manual operations with constant retrenchment, associated training challenges, and the need for higher supply chain visibility are here to stay, regardless of the current economic situation. This is prevalent in Asia, where corporations have only recently started driving this initiative after the impact of the COVID-19 pandemic and the various recent supply chain challenges.
“However, we expect that customer expectations from the same investment will increase. This requires products capable of delivering high levels of throughput with minimal downtime. This has always been a prime focus for our engineering work at Botsync, and with our syncOS developments, we are well positioned to deliver on this,” Nambiar concludes.
—
Fundraising or preparing your startup for fundraising? Build your investor network, search from 400+ SEA investors on e27, and get connected or get insights regarding fundraising. Try e27 Pro for free today.
The post Botsync’s automatic mobile robots want to lift APAC’s logistics sector to the next level appeared first on e27.
Discussion about this post